Thoroughly Tested for Your Safety
Whether it be in machine and plant engineering, robotics or industrial automation, our cables and wires are exposed to high dynamic loads in many applications. Repetitive bending and torsional movements put considerable stress on the materials used. Nevertheless, users expect our products to be reliable, long-lasting, perform consistently and prevent system malfunctions, failures and safety risks.
For this reason, HELUKABEL subjects its cables and wires to extensive tests and inspections. In the testing laboratories at our production facility in Windsbach, Germany, we use ultra-modern equipment to simulate the stresses applied to our cables and wires, which exceed those encountered in application. In this way, we ensure that every product consistently meets the high demands of our customers, and that you always receive the quality that you expect from us as a leading supplier of cables, wires and accessories for more than 40 years.
Some of the testing our cables undergo are:
Learn more about each type of test below.
Bending Tests
Bending tests are used to evaluate the mechanical strength of cables and wires under bending stress. In application, frequent directional changes over time may lead to cable breaks, especially at weak points. With our testing equipment, we simulate various loads and bending radii to ensure that our products reliably withstand the stresses and strains that come with everyday use.
Click here to read more about bending, why we test it, and how it affects cable performance.
Alternating Bending Tests with Two Reels | Alternating Bending Tests with Three Reels |
• Test in alignment with DIN EN 50396 6.2 • Max. speed: 4 m/s (Target: constant speed of 0.33 m/s) • Max. acceleration: 6 m/s² • Max. movement distance: ±160 cm | • Tests in alignment with DIN EN 50396 6.3 • Max. speed: 0.5 m/s (Target: constant speed of 0.1 m/s) • Max. acceleration: 3.5 m/s² • Max. movement distance: ±70 cm |
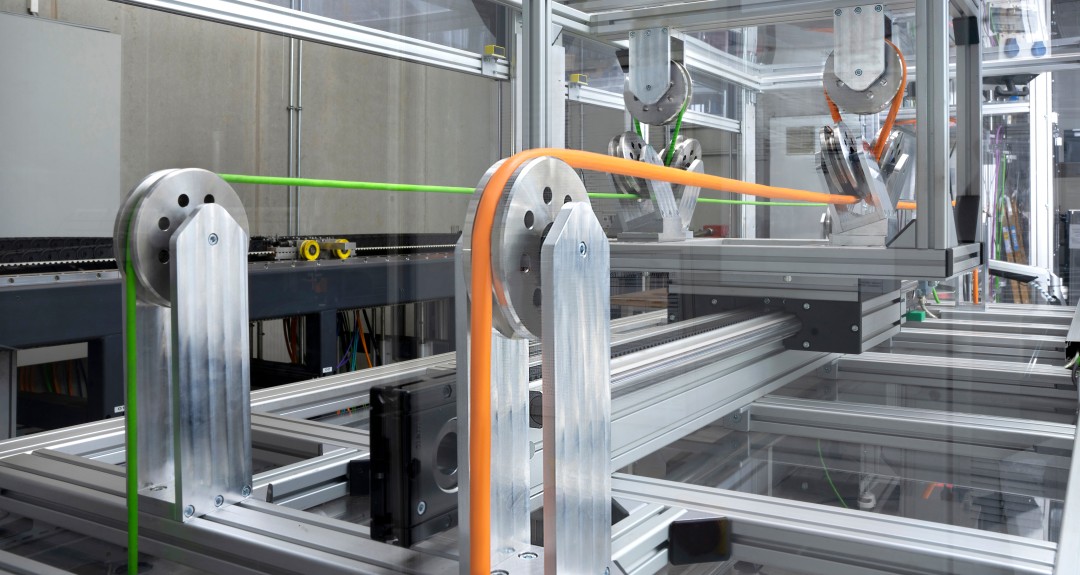
Abrasion Tests
Cables used in dynamic applications are exposed to a variety of mechanical stresses – including abrasion due to contact with other machine components, for example. Over the long term, this may damage or destroy the insulation of a cable and can even result in cable breaks, malfunctions, short circuits and fires. Therefore, we run abrasion tests in our testing laboratories, to evaluate the suitability of our jacketing and insulation materials against the demands of everyday use.
Click here to read more about abrasion, why we test it, and how it affects cable performance.
Abrasion Test Equipment
• Max. speed: 0.44 m/s
• Max. acceleration: 2 m/s²
• Clamping length: ±25 cm
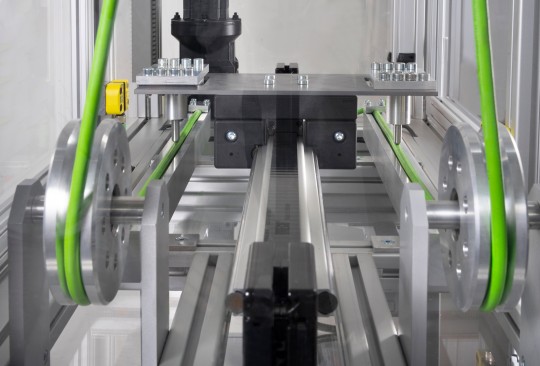
Kink Tests
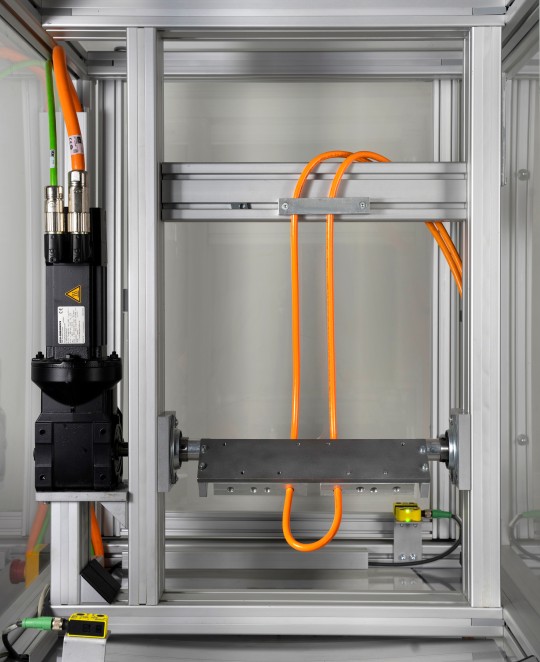
Bending loads are part of everyday life for cables and wires in many moving applications. Over time, however, they can irreparably damage jacketing and conductor materials and even lead to a break, which can result in expensive malfunctions, machine failures and fire hazards. To avoid these issues, we run special kink tests to assess a cable’s resistance and avoid unexpected surprises when used.
Click here to read more about kinking, why we test it, and how it affects cable performance.
Kink Test Equipment
• Max. speed: 440°/s
• Max. acceleration: 2000°/s2
• Max. torsion angle: ±180°
• Clamping length: 50 cm
Torsion Tests
Cables applied to industrial robots and other moving machines must often withstand extreme torsional loads. We simulate this type of stress around the cable’s axis in our testing facilities. This is how we ensure that all materials used are reliable and long-lasting. Click here to read more about torsion, why we test for it, and how torsion affects shielded cables.
Kaeppner Torsion Test Equipment | Audi Torsion Test Equipment |
• Max. speed: 1000°/s • Max. acceleration: 775°/s² • Max. torsion angle: ±720° • Max. clamping length: 200 cm • Min. clamping length: 30 cm | • Max.speed: 440°/s • Max. acceleration: 2000°/s² • Max. torsion angle: ±360° • Clamping length: 100 cm |
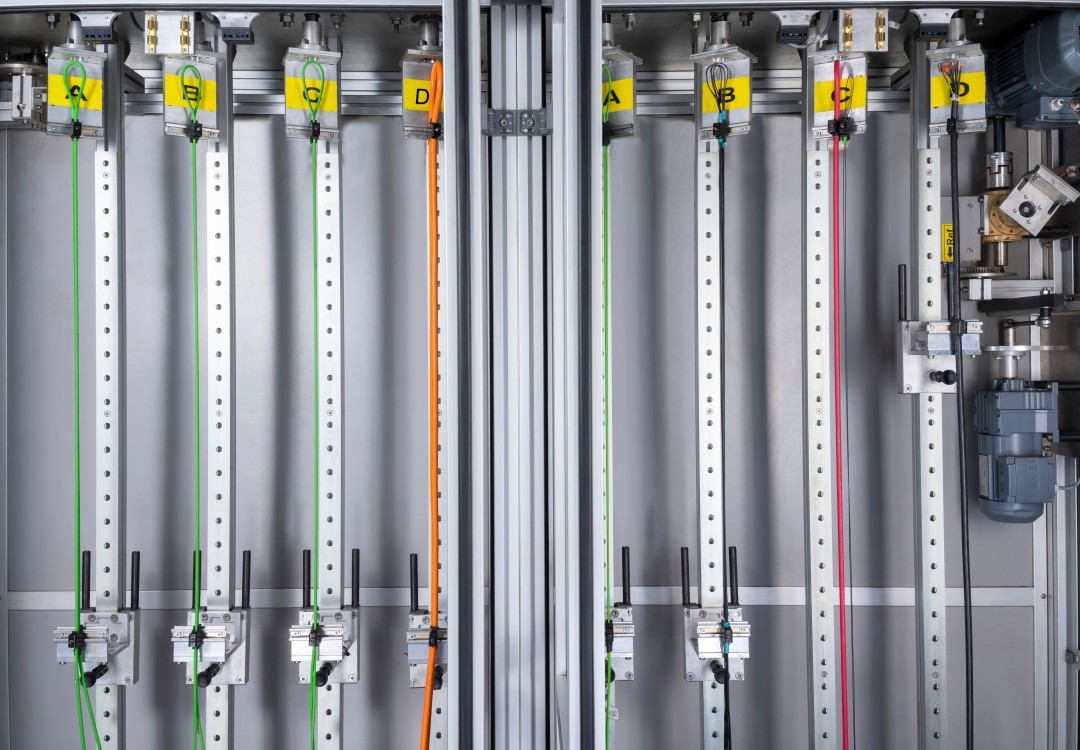
Wind Turbine Torsion Testing
Cables in wind turbines are also exposed to strong torsional forces. This may cause their mechanical and electrical functionality to deteriorate over time. We check the torsion resistance of our products in our test tower for wind power cables to prevent expensive system failures once in use.
• Height: 8 m
• Max. speed: 0.8 U/min (288°/min)
• Twist: ±150° per meter loop
• Loop height: 6 m (results in a rotation of ±900° per cycle)
Click here to read more about torsion, why we test for it, and how torsion affects shielded cables.
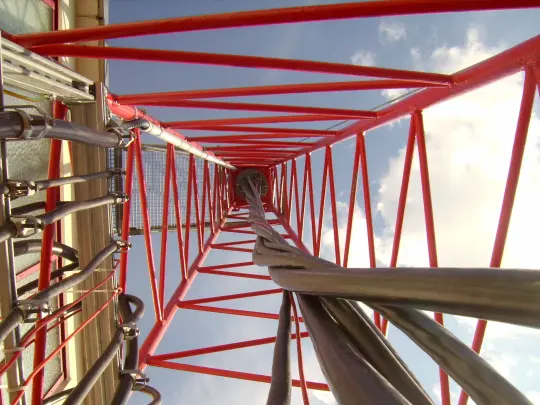
Drag Chain Tests
Drag chain cables are always on the move: high accelerations, tight bending radii and constant abrasion are continuous strains on the material. Our drag chain test systems allow us to apply different travel distances and chain radii, which allows us to simulate various operating conditions.
Click here to read more about drag chain dynamic loads, why we test for it, and how it can affect cable performance.
Our Drag Chain Test Equipment at a Glance:
Test 1 | Test 2 | Test 3 | Test 4 | Test 5 | |
Max. acceleration | 50 m/s² | 50 m/s² | 50 m/s² | 2 m/s² | 30 m/s² |
Max. speed m/s | 5 m/s | 5 m/s | 10 m/s | 4 m/s | 10 m/s |
Max. movement distance | 0.9 m | 3 m | 5 m | 18 m | 20 m |
Number of chain radii | 2 | 4 | 4 | 4 | 8 |
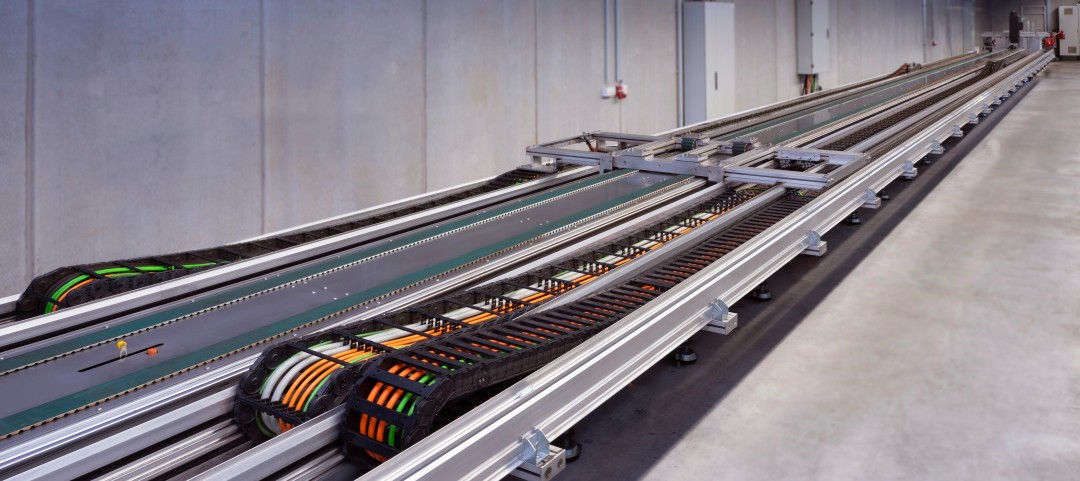
Twister Test
There are applications where our cables and wires are exposed to torsional and bending movements at the same time. For this reason, we have a twister test that applies both torsional and bending stress with a special drag chain that simulates the loads applied in highly dynamic applications. The travel distance and the maximum angle of rotation are specified by the drag chain.
• Max. speed: 480°/s
• Max. acceleration: 5000°/s²
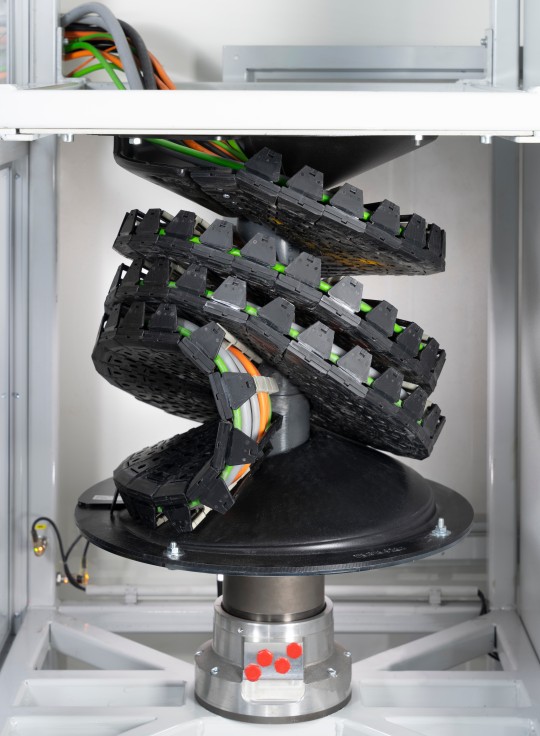