Power Supply in a Confined Space
Siltronic equips a new wafer production plant in Singapore with connecting cables from HELUKABEL
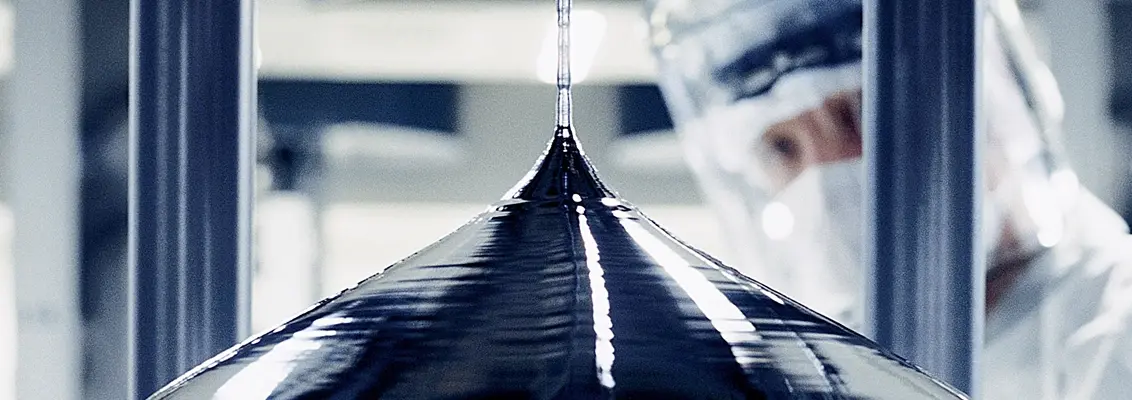
Wafer manufacturer Siltronic’s new production facility has a large number of production machines. There is often little space for the power connection - this requires flexible cables with small bending radii. Thanks to the support of HELUKABEL Singapore and the PVC control and connection cables of the HELUPOWER® 1000 RV-K series, the semiconductor specialist can rely on the reliable operation of its machines.
From smartphones and computers to modern cars, medical technology, machine tools, solar and wind power plants, countless technological achievements of recent decades would not have been possible without a tiny, inconspicuous component called a microchip. Integrated circuits are able to perform complex logic operations and calculations in a very small space, which is the basis for the functioning of all electronic devices.
The basis of microchips are wafers. These are round or square slices of silicon less than a millimeter thick where the required transistors, capacitors and other resistive elements are deposited and combined to form a circuit. Demand for wafers has been growing rapidly for decades. This is due to increasing digitalization and the introduction of electronics into more and more areas of application.
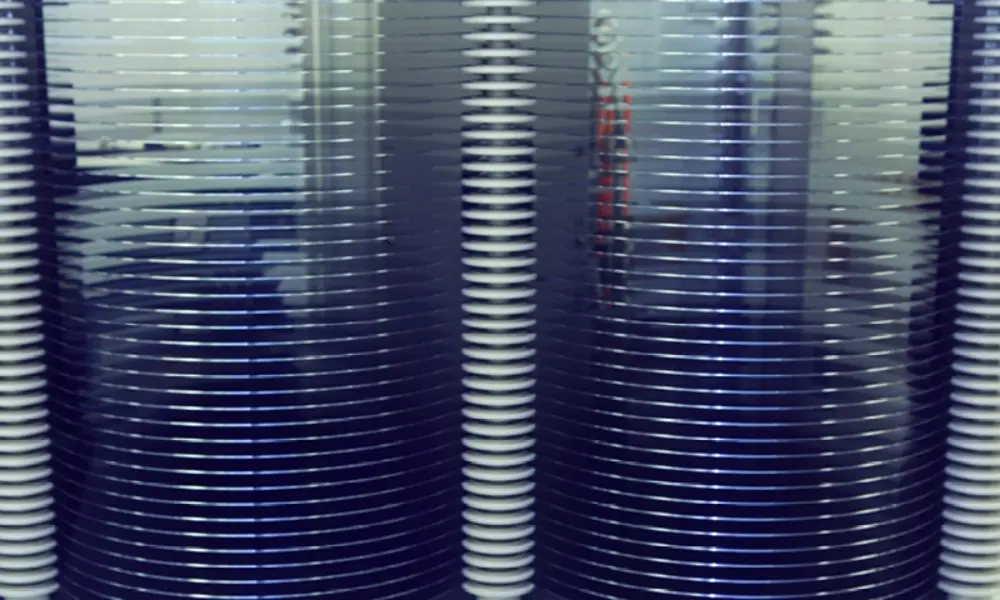
Wafers are round or rectangular sheets of silicon that are less than a millimeter thick. They are the basis for microchips.
Siltronic AG is one of the leading manufacturers of silicon wafers. The Munich-based company has existed in its current form since 2004, but its origins date back to the 1950s when it began researching and developing ultra-pure silicon. Today, Siltronic employs nearly 4,500 people, has facilities around the world, and produces an average of one wafer per second. The strategic focus is on the production of wafers with a diameter of 12 inches (300 millimeters), the size of which makes them suitable for high-tech applications such as graphics cards in computer technology.
Largest investment in the company's history
The largest and most modern production facility for these products to date is currently being built in Singapore. This is the biggest investment in Siltronic's history. Around 600 new jobs will be created to expand production capacity to meet the growing demand for semiconductor devices. Ground was broken in 2021 and construction is now well underway.
Wafers are made from blocks of semiconductor material, known as ingots, and undergo numerous processing steps before they are finished. Siltronic's machinery is correspondingly extensive, ranging from the sawmill to surface finishing. To power the machines, the building has an extensive electrical infrastructure that provides various voltages up to 66 kilovolts at numerous connection points. It is Anton Waltl's job to connect the machines to these points. The project engineer at Siltronic Singapore and his team ensure that all the production equipment has the power it needs to operate.
Flexible installation in hard-to-reach areas
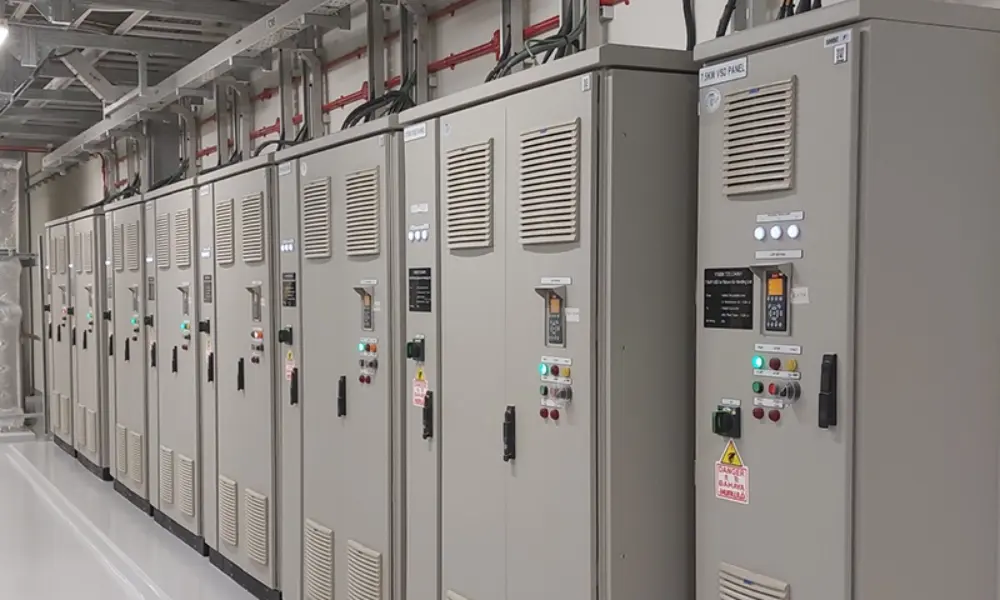
To power the machines, the building has an extensive electrical infrastructure.
"We use connection cables with different numbers of conductors, cross sections and nominal voltages to supply power to the machines," says Waltl. "However, one challenge is often the same: the limited space and hard-to-reach connection areas where we have to install the cables. It is crucial that the cables are suitable for tight bending radii. "Otherwise there is a risk of damage or even cable breakage, which can lead to expensive production downtime," explains Waltl.
During his time in Germany, the project engineer had already had good experiences with HELUKABEL as a partner for electrical connection technology - so it was obvious to bring the specialist on board for the new building in Singapore as well. "HELUKABEL is represented here by a local subsidiary, so the company was able to offer us the desired service and fast response times," says Waltl, explaining his choice. "Especially with a project of this size, it is a considerable advantage to have a contact person nearby who knows the local market and the applicable regulations inside out, and who can also respond quickly to short-term requirements".
Reliably high product quality
However, it was not only the service that was convincing, but also the products. With the PVC control and connection cables of the HELUPOWER® 1000 RV-K series, HELUKABEL offers high-quality power cables for machines and devices, which, among other things, impress with their high flexibility. Depending on the size, they have a minimum bending radius of only four times the outer diameter. "Local cable manufacturers here in Singapore do not offer such cables in this form," says Waltl. The HELUPOWER® 1000 RV-K is flame-retardant and resistant to UV radiation, ensuring long-term reliable machine operation. "We also benefit from the fact that the cables are manufactured in accordance with all applicable regulations and are of consistently high quality. This creates security of supply, which is an important factor for us," emphasizes Waltl.
Saved assembly times
HELUKABEL is also supplying motor cables from the TOPFLEX® range, single conductors from the NSGAFÖU range, and many other products for the new Siltronic plant. Anton Waltl and his team also like the way the cables are made: "The cables are easy to handle and pull thanks to their smooth surface. This saves us a lot of time during installation. This is also an important aspect for those responsible at Siltronic, because the machines often have to be commissioned quickly. The semiconductor specialist will continue to rely on HELUKABEL for further production site expansions. Waltl is fully confirmed in his choice: "We are very satisfied with the cooperation and look forward to bringing this project to a successful conclusion together".
You can find this and many other exciting articles in the current issue of POWER, our customer magazine POWER. Read it now !