Sturdy Guidance for Accurate Measurements
EKD Systems supplies customized drag chains for KARL DEUTSCH ultrasonic testing systems.
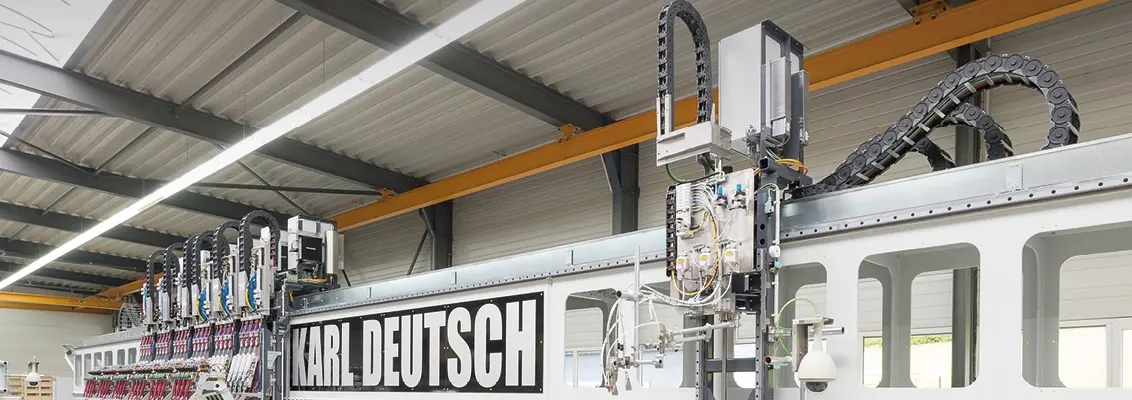
The ultrasonic testing systems from KARL DEUTSCH Testing and Measuring Equipment Manufacturers GmbH + Co KG detect the smallest welding defects generated during the manufacturing of steel pipes. The measuring equipment used to do this is extremely sensitive and must deliver accurate results despite the long travel distances and high speeds of the system. Each vibration can corrupt the measurement results and impair production quality. HELUKABEL subsidiary EKD Systems supplied customized drag chains for this demanding application. Their high stability guarantees accurate measurements with fewer errors and reliable functionality over the entire lifetime.
One of the oldest methods for producing steel pipes is welding. Rolled steel sheets are formed into circular cross-sectional lengths whose ends are then joined together. Although other sheet metal forming processes exist these days for making seamless pipes, two-thirds of the steel pipes manufactured in the world are still welded. The technologies for doing this have steadily evolved over the years. The High Frequency (HF) method, for example, has been around since the 1960s. This method uses high-frequency currents to generate high levels of heat. Fast welding speeds and good efficiency are the distinguishing features of this method.
To guarantee the quality of the welded pipes, the weld seams are controlled during production by a non-destructive test procedure such as ultrasonic testing. Here, a test head sends sound waves through the material and records their reflections. The ultrasonic device creates an image that reveals the smallest of weld seam defects. The method is exceptionally precise but equally sensitive.
Sensitive measurements at high speed
An expert in this specialist field is KARL DEUTSCH Testing and Measuring Equipment Manufacturers GmbH + Co KG. The company, headquartered in Wuppertal, Germany, has dedicated itself to the development and production of equipment for the non-destructive testing of materials since it was founded in 1949. Its portfolio includes ultrasonic testing systems such as the Echograph SNHF which can be used to test HF-welded pipes for production defects. “Our machines must be able to carry out sensitive measurements, even over long travel distances at high speeds,” points out Holger Harmuth, Machine Tool Manufacturing Designer at KARL DEUTSCH. “A low-vibration environment is extremely important here to avoid distorted measurement results.”
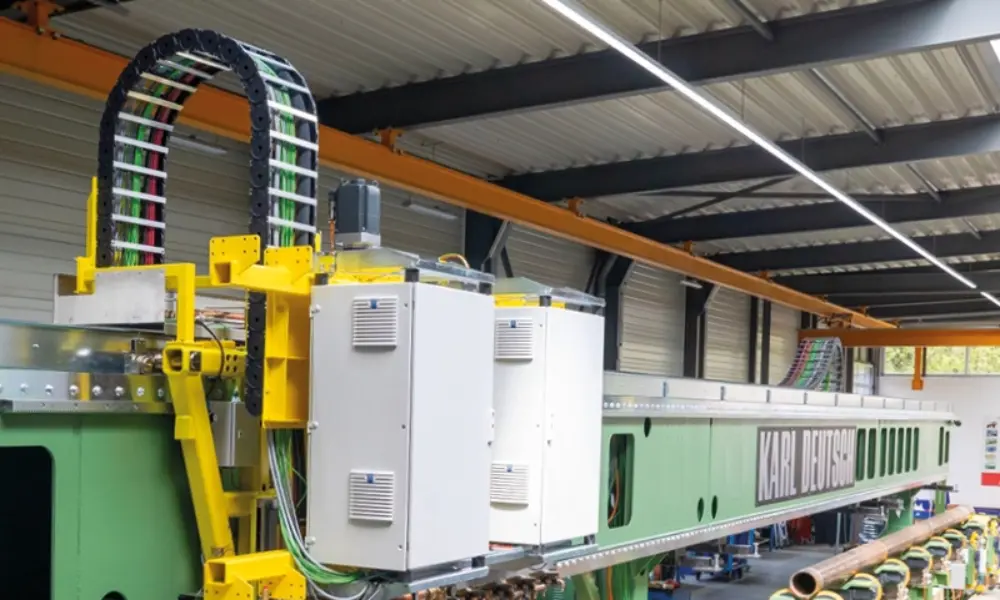
The moving parts of the system are fitted with drag chains from EKD Systems.
The moving parts of the system are fitted with drag chains. These contain the cables that supply the individual components with power, data and control signals. The cable carriers protect the cables from getting tangled or trapped during operation or from becoming damaged as a result of abrasion and tensile loading. “Many off-the-shelf drag chains cause vibrations when they move which can corrupt the results of our measurements,” explains Harmuth. When KARL DEUTSCH started planning a new version of the Echograph series, they commissioned the experts at EKD Systems, a HELUKABEL Group subsidiary, to supply bespoke drag chain systems for this sophisticated application.
Challenges such as these are nothing out of the ordinary for EKD Systems since the company has been specializing in the development and production of customized steel, stainless steel and plastic drag chains for more than 50 years. Their focus is on user-specific system solutions designed to customer requirements, in small to mid-sized quantities. For this, EKD Systems has a number of machining centres, its own tool and die-making facilities, as well as a broad-based fully automated plastic injection molder. “We have a vast array of diverse drag chain systems in our assortment that can be modularly adapted to the individual requirements of our customers,” explains Karsten Göbel from Technical Sales at EKD Systems.
The drag chains used in the KARL DEUTSCH ultrasonic testing system need to be particularly sturdy. The experts from EKD Systems therefore opted for the PLE plastic link drag chain. This is a plastic hybrid chain with rugged aluminum dividers and a multiple locking system in the joints to ensure high stability and safe guidance of the cables. The chains are also suitable for long travel distances and high travel speeds and therefore optimally support the dynamic performance of the testing system. EKD Systems has also fitted sliding elements into the inner radius of the chain to reduce the driving forces. The result is a version of the chain that guarantees smooth and precise transmission of forces and movements, and hence reliable measurement operations.
Bespoke carrier for tight installation spaces
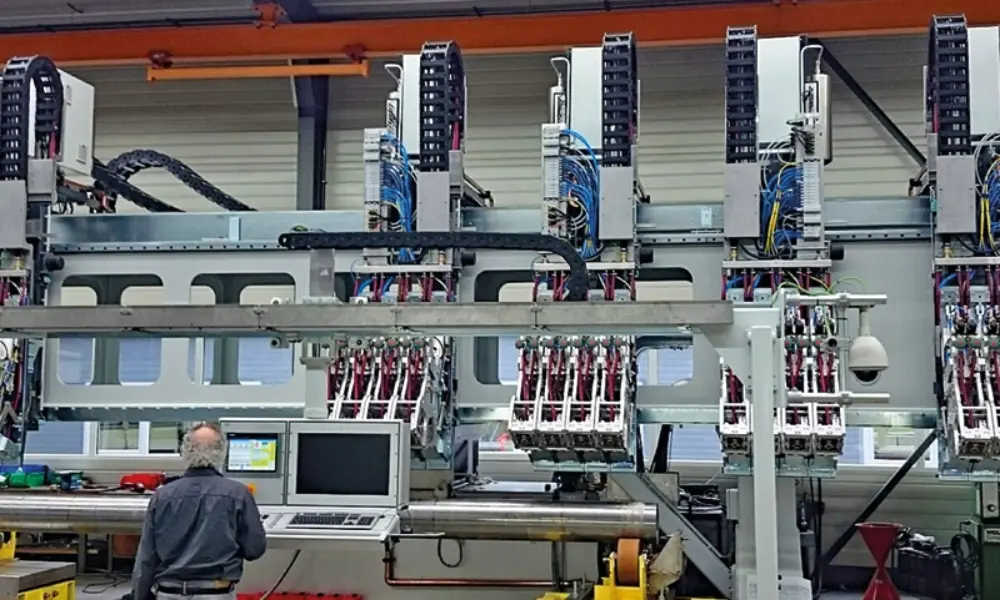
The customized drag chain system facilitates accurate measurements and reliable functionality of the testing system.
A cable carrier optimized for installation in tight spaces was an additional requirement alongside extremely smooth operation. The testing system has a travel distance of 27 meters and a travel speed of 2 meters per second – and that in a very confined space. To make optimal use of this space, EKD Systems created a customized drag chain system comprised of a trough made to customer specifications that fit perfectly into the existing design. The special construction of the chain uses dividers to facilitate a highly variable design of the inner space. This optimizes the cable carrier and contributes to the reliable functionality of the testing system.
After setting up the machine at the KARL DEUTSCH factory, it was dismantled into its components in preparation for transport to the end customer. The cables were inserted into the drag chain by EKD Systems and then wound onto a special assembly reel included in the scope of delivery. “This facilitates fast and efficient on-site installation of the chain, which saves a lot of time and money during the assembly of the system,” recalls Harmuth.
Tailored exactly to the application
Thanks to the cooperation with EKD Systems, KARL DEUTSCH received a customized pre-manufactured drag chain system tailored exactly to the specific requirements of this sophisticated application. “The rugged and low-oscillating drag chain facilitates the precise transmission of force and movement and hence accurate measurements with fewer errors and reliable functionality of the testing system over the entire lifetime,” praises Harmuth, who is completely satisfied with the partnership. “Together with the experts from EKD Systems we were able to build a first-class product that saves both us and the system operator considerable time and money.”
You can also find this and many other exciting articles in the current issue #14 of our customer magazine POWER. Read it now!