Q&A With HELU: Cables for the Production of Biogas
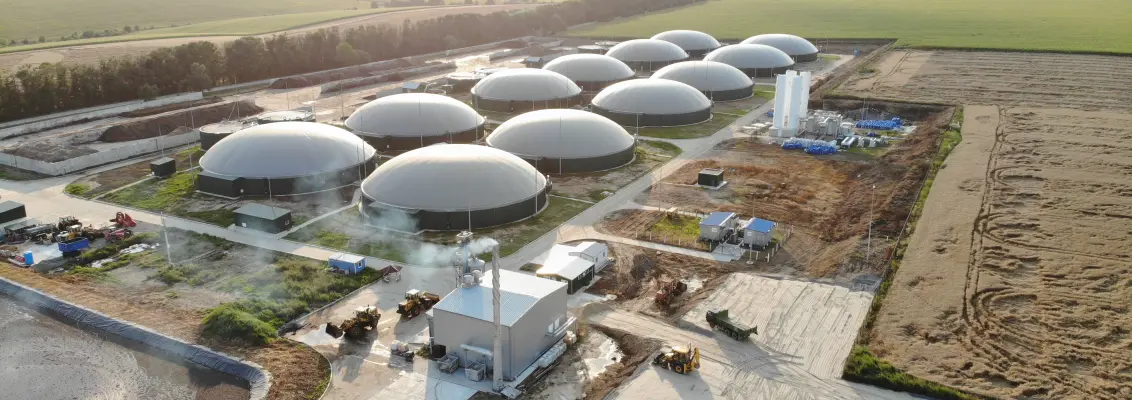
The biogas industry involves the production of biogas through the anaerobic digestion of organic materials such as agricultural or municipal waste. Biogas and biomethane are considered the fastest-growing forms of bioenergy. Their combined market share in total demand is anticipated to be between 12 – 20% by 2040, according to the International Energy Agency.
Biogas production plants are very useful as they can fill gaps in the power grid because they can provide power immediately when needed. Additionally, since they are typically installed decentralized near farms their ability to be activated to meet unexpected energy gaps compared to centralized gas turbine or coal-fired power plants is much easier.
In this Q&A With HELU, we take a look at this growing source of energy and the systems and cables needed to keep operations running smoothly.
Q: What is biogas and how is it produced?
A: Biogas primarily consists of methane (CH4) and carbon dioxide (CO2), with trace amounts of other gases like hydrogen sulfide (H2S). The methane component is what makes biogas a valuable renewable energy source, as it can be used for heating, electricity generation, or as a fuel for vehicles after purification.
Biogas production technology takes organic materials such as agricultural waste, manure, municipal waste, plant material, sewage, green waste, or food waste and pumps it into anaerobic digesters, where fermentation begins under oxygen-free conditions. Once fermentation is complete, it is sent to a gas upgrading unit to create biogas. The process also produces a nutrient-rich byproduct called digestate, which can be used as a fertilizer. Anaerobic digestion is not only an effective way to produce renewable energy but also helps in waste management and reduction of greenhouse gas emissions from organic waste.
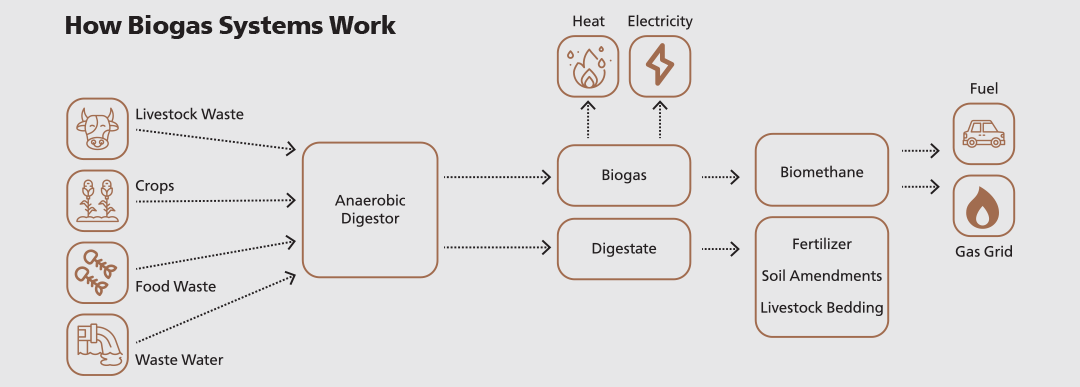
Q: What equipment and machines are used in biogas production and what cables are needed for their use?
A: Biogas production involves a series of processes and thus requires various types of equipment and machinery. Each piece of equipment has specific cabling needs for power supply, control and data transmission. Below is a table that summarizes various applications found in a biogas plant, the equipment used, and related cables one would find.
Application | Equipment Used | Cables Required |
Feedstock Preparation Equipment | Choppers, grinders, mixers and conveyors for preparing and transporting the organic material into the digester. | Heavy-duty power cables for motors, control cables for operation, and data cables for monitoring feedstock input. |
Anaerobic Digesters | Sealed tanks where the biogas is produced. | Temperature control cables, power cables for heating systems, and sensor cables for monitoring pressure, temperature and gas composition. |
Gas Collection and Storage Systems | Gas holders and storage tanks. | Power and control cables for gas compressors and pumps, and data cables for monitoring gas volume and pressure. |
Gas Cleaning/Upgrading Equipment | Scrubbers, filters and separators to remove impurities like H2S, CO2 and water vapor. | Power cables for operating cleaning equipment, and sensor cables for monitoring gas purity and composition. |
Cogeneration/CHP Units | Combined heat and power (CHP) units that generate electricity and heat from biogas. | Power cables for generators, control cables for managing power output, and data cables for performance monitoring. |
Control Systems | Programmable Logic Controllers (PLCs) and computer systems for plant automation and control. | Data communication cables for network connectivity, control cables for interfacing with different equipment. |
Pumping and Piping Systems | Pumps and pipelines for moving feedstock, digestate and biogas. | Power cables for pumps, and control cables for valves and flow meters. |
Digestate Processing Equipment | Separators, dryers and storage for post-digestion material. | Power cables for conveyors and dryers, control cables for operation, and sensor cables for moisture content monitoring. |
Safety and Monitoring Systems | Gas detectors, fire alarms and surveillance systems. | Low-voltage power cables, data cables for connectivity, and control cables for alarm systems. |
Auxiliary Systems | HVAC, lighting and emergency systems. | Power cables for lighting and HVAC, control cables for system operation. |
Q: What mechanical and environmental considerations should be taken into account in a biogas plant?
A: Depending on the area within the plant or the specific application, cables will be faced with various mechanical or environmental stressors. A few aspects to consider are:
- Chemical Resistance: Given the exposure to various chemicals and corrosive substances, cables should be resistant to chemicals. Materials like polyethylene or fluoropolymers are often used for insulation and jacketing.
- Moisture and Waterproofing: In biogas plants, a higher ingress protection (IP) rating is desirable to protect against humid and often wet conditions to protect against moisture and water ingress. IP is relevant for cable entry points into machines such as glands, but to ensure a uniform seal cable jackets need to be concentric and not convoluted.
- Mechanical Durability: Cables should be able to withstand mechanical stresses like abrasion, crushing, or bending. This is particularly important in areas with heavy machinery or where cables may be subject to frequent movement.
- Temperature Resistance: Electrical connection technology must withstand the temperature variations they will be exposed to. This is particularly important for areas near digesters or engines where temperatures can be high.
- Electromagnetic Compatibility (EMC): As systems become more automated more cables will be used for power and data transmission. Cables must be properly shielded with either braids, foils or a combination of both so they do not emit excessive electromagnetic interference and are immune to external interference, which is crucial for accurate data transmission.
- Voltage and Current Ratings: Cables must withstand the various voltages and currents they will carry depending on the application, e.g. motor power or temperature data monitoring, ensuring they can safely handle the electrical load without overheating or degrading.
Q: Why is component reliability and minimizing downtime important with biogas plants?
A: Like all manufacturing, machines that are down do not benefit the plant. Due to manufacturing conditions, such as unpleasant odors or the need to be close to raw materials, many plants are built in remote areas where easy access to replacement parts is difficult to acquire quickly, especially if they are not kept in the MRO building. This means that machines and components must withstand the rigorous plant conditions to optimize their longevity. When specifying cables and wires for the plant, it is vital to know what conditions the cable will be primarily operating in to ensure the correct jacket compounds and insulation materials are chosen . For example, the cables supplying power to the equipment’s motors as well as those transporting power to the generators often experience strong vibrations that can wear cable jackets down over time. In applications similar to these, PUR-jacketed cables tend to be more commonly used than standard PVC since they have high abrasion resistance in addition to strong chemical and fluid resistance characteristics.
Q: What safety standards must power and data cables meet in a biogas processing plant?
A: In a biogas processing plant, power and data cables must adhere to a variety of safety standards to ensure they can operate safely and efficiently in this unique and potentially hazardous environment. These standards typically address issues like fire resistance, chemical resistance, mechanical durability, and electrical performance. A few key aspects include:
- Explosion Protection: Due to the presence of methane and other flammable gases, cables must conform to explosion protection standards like NEC Class I, Division 2 in the United States or ATEX in Europe. These standards ensure that the cables can operate safely in environments where explosive gases may be present.
- Fire Resistance: Cables should be fire-resistant to prevent the spread of fire. Standards such as the International Electrotechnical Commission (IEC) 60331, Underwriters Laboratories (UL) 94, and Canadian Standards Association (CSA) FT4 rate cables based on their resistance to fire exposure.
- Compliance with Local and National Codes: Finally, all cabling must comply with local and national electrical codes, such as UL 758 (AWM), 1277 or 2277, NFPA 79, or CSA C22.2 No. 230 or 239. These codes ensure that the installation and the materials used meet specific safety criteria.
ARTICLE DOWNLOAD
Click here to view this article in our digital download centre.