Pressed for Time

The technique of turning sheets of metal into a useful part or component is called sheet metal stamping and is one of the first stages in the automotive assembly process. The metal is fed into a press, where the stamping tool, also known as a die, creates the desired shape. The die is pressed into or through the metal with tremendous force and is used to create such parts as doors, hoods, fenders, chassis rails, tailgates, and roof panels, to name a few.

One of the largest metal stamping press manufacturers in North America was recently awarded a contract to install multiple presses at a new automobile manufacturing plant. As with most construction projects, there was a very tight installation schedule for the presses. The project had already been delayed due to unforeseen issues with the plant’s overall infrastructure at the job site. To get back on schedule, the press manufacturer began a search with the aid of their supply chain partner to source the necessary cabling required for the project. One specific motor cable was deemed critical to the project timeline because it would provide the primary power for the presses. The process of identifying potential suppliers for this cable got underway. HELUKABEL was contacted and asked to provide a quotation based on specifications shared by the customer. Given the importance of the project, it was revealed that the same information had been provided to 10 other cable suppliers.
The cable required for the press installation was one that is not commonly produced for stock and would be subject to a new production run based on the quantities needed. The customer had specific requirements for the overall outside diameter of the cable as well as the need for it to be flexible in order to accommodate working in tight spaces. Initially, the qualification process required the submission of detailed product specifications as well as a cable sample. This process became more time-consuming as the samples and documentation had to be shared by the customer internally with team members located in different parts of the world.
Upon approval of the specifications and samples, HELUKABEL was asked to provide a quote and delivery time. The bid process was competitive as other potential vendors were also approved. Finally, after comparing all the bid packages submitted, HELUKABEL was chosen for the project to supply it’s TOPFLEX® 1000 VFD cable. This shielded, motor power cable with Class K-stranded conductors and a three power plus three (3+3) symmetrical ground configuration met the customer’s flexibility and outside diameter requirements. Additionally, the lead time was a much better fit for the timeline set by the customer compared to other suppliers being considered.
Soon after placing the order, a new challenge appeared – there were going to be limitations on the reel sizes and weights to accommodate transporting the cable to the job site. More importantly, the customer also required special cable packaging and labeling to properly distribute it to the necessary locations once onsite. Due to the early job site delays, the project timeline had been moved up by the end user and the press manufacturer needed help with both an expedited delivery as well as any ideas that would provide time and labor savings at the manufacturing plant.
HELUKABEL engineers came up with the idea to put multiple cut lengths of cable on the reels, with each cut being specifically labeled to designate a location for installation for each press. This would allow the installation crews to move the reels efficiently along the press lines on the factory floor and avoid the possibility of costly mistakes that could occur by cutting and labeling the cable onsite. This idea was approved and detailed cutting and labeling instructions were provided to HELUKABEL’s warehouse team. The special packaging would include over 70 cut lengths of cable and 140 custom labels across multiple reels.
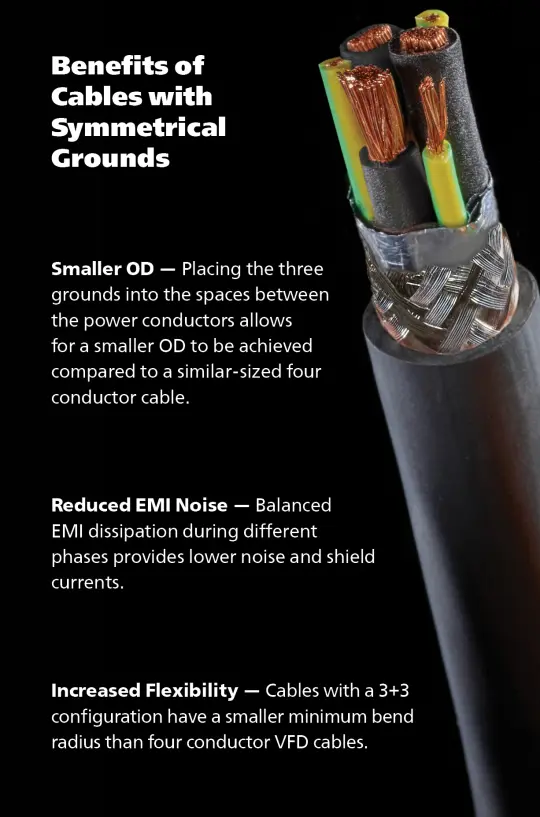
The cable was delivered within the project guidelines and the customer was extremely satisfied with the custom packaging and labeling of the TOPFLEX® 1000 VFD. The onsite installers confirmed that the packaging allowed for a seamless installation with very little waste.
HELUKABEL’s ability to provide customer-focused ideas allowed it to not only become a trusted partner to a global machine manufacturer, but it was also awarded the next phase of the project to supply the same TOPFLEX® 1000 VFD cable for power as well as several sizes of our TRAYCONTROL® 600 cable to be used for various controls throughout the presses.
ARTICLE DOWNLOAD
Click here to view this article in our digital download centre.