A 360° Safety Net for Mining Vehicles
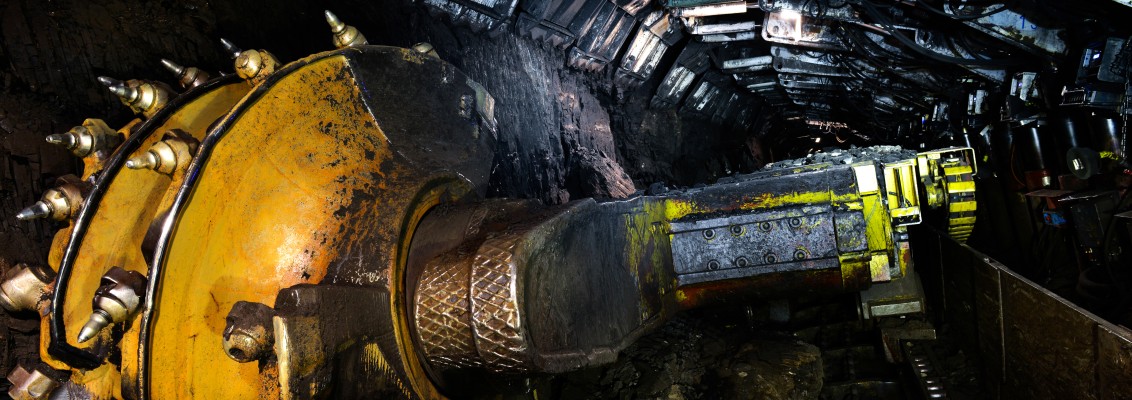
The mining industry has a long and storied history, but it has always been considered one of the more dangerous enterprises on the planet.
Although mining operations are now much safer for workers than in the past, miners continue to face hazards daily. The most common health and safety risks include cave-ins, collapses, fires, explosions, dust, exposure to loud noises, and heavy equipment/vehicle accidents.
Mining in the Past
The first mine shafts were dug out by hand or using stone tools, a slow and time-consuming process. This then transitioned to using enhanced tools such as the pick and hammer. In the late Middle Ages, miners furthered their techniques to include blasting with black powder to break up large rocks. Black powder was eventually replaced with dynamite in the mid-19th century. While this was happening, motorized mining tools – drills, lifts and steam-powered pumps – were being developed.
The Industrial Revolution brought about improvements in both explosives and the equipment used to break up rock and expose precious metals and gems. Mechanical drills, once powered by pistons, changed over to compressed air, which significantly increased their capability and efficiency of mining hard rock. Loading and hauling by electric conveyors, mine cars, and vehicles replaced inefficient methods such as rope and pulleys or animals. Steam-driven pumps solved the problem of water inflow. Overall, new mechanical technology sparked dramatic improvements in mining techniques.
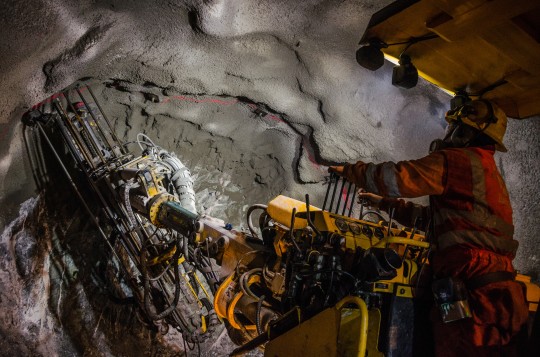
Mining Technology Today
In order to overcome the many safety challenges and maintain production, mining companies and the miners themselves have to embrace a wide variety of safety solutions. General safety procedures and personal protective equipment were the dominant approaches to eliminating hazards in the past, but advances in remote-controlled mining equipment, proximity sensors and automation have taken this to another level.
Autonomous technologies are bringing a heightened measure of safety to mines as well. Advances in the capabilities of robots and automated machines have made it possible to take over activities traditionally carried out by human-controlled machinery. From self-driving trucks to robotic hauling, drilling, and other processes, autonomous equipment boosts the efficiency of operations and increases safety by removing workers from hazardous situations.
The use of internet of things (IoT)-linked wearables can be used to detect environmental conditions, the location of workers, and monitor the fatigue levels of vehicle operators. These devices relay an early-warning signal for potentially harmful or dangerous situations, thereby reducing risks and preventing accidents.
Radio-frequency identification (RFID) tags are increasingly being used to track assets underground – whether human or vehicular. These tags are used to pinpoint the location of workers and equipment within the mine in real-time, while also tracking their movements. RFID systems can also monitor usage patterns of heavy equipment. This information can be used to help schedule part replacement or fluid changes thereby optimizing equipment maintenance.
The Opportunity
Mine shafts today are much larger than at any time in history. This enables much larger equipment to be used in the extraction of materials. These machines include bulldozers, front loaders, off-road dump trucks, and cranes.
The operators of these pieces of equipment are required to work safely and efficiently in 24-hour shift patterns, sometimes in close proximity to another vehicle. For example, an excavator could be working next to a large dump truck to remove blast debris, which could be a risky situation.
HELUKABEL was approached by a manufacturer of vehicle proximity technology that can be installed on mining equipment to regular vehicles, like off-the-lot pickup trucks. This range of equipment – from cameras and monitors to sensors and digital recorders – can be applied to the front, sides and rear of the vehicle, giving the operator a 360-degree field of view. The system is capable of making audible announcements including “Door Not Shut”, “Objects Outside the Vehicle”, or providing seatbelt notifications. In more extreme cases, it can apply the brakes or shut down the vehicle. These devices help the driver to operate the machinery safely while working efficiently around the clock.
For these devices to work properly they need to be interconnected by cables that can withstand the environmental and mechanical challenges found within a mine since the cables are most often installed along the vehicle’s exterior. The manufacturer requested that any cable solution offered must satisfy the following requirements:
• Low Smoke Zero Halogen — The demand for a cable that is halogen-free revolves around a mine’s risk to fires. In the event of a fire, miners and equipment operators would be exposed to significantly less smoke and toxic gases filling up their space-restricted areas.
• Withstand a 20-joule impact — A 20-joule impact can be tested using a 10-pound weight being dropped on the cable from a height of 1.5 feet. This is done 10 times. A failure is a loss of continuity or shorting between the conductors or shield. A cable that can pass this test will be able to withstand being struck by debris that a vehicle could encounter within the mine.
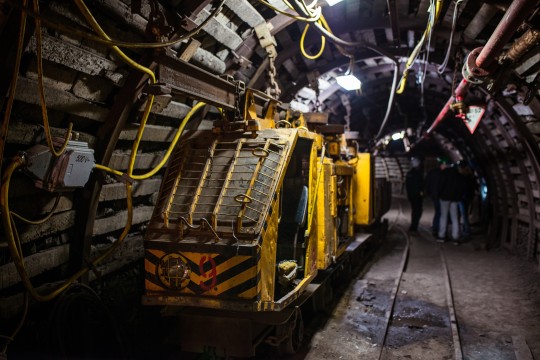
• Shielded — Shielded cables act to reduce the volume and intensity of all kinds of electrical noise and EMI, decreasing the adverse effects caused by signal transmission loss. The importance of shielded cables in mines can’t be stressed enough. Shielding not only protects the cable but also can protect machinery and other people as well. In an application that is underground and in tight quarters, equipment meant to help prevent vehicles from colliding with other equipment or people could potentially have the opposite effect, if they aren’t working properly.
• UV resistant — While the vehicles being retrofitted by the manufacturer will be primarily used underground, they will periodically be parked outside. UV resistance is important so that the cable doesn’t degrade when exposed to direct sunlight.
• Abrasion resistant — In a mining environment, the vehicles will encounter gravel, dirt and other abrasive materials. The cable used needs to be resistant to such objects. Incidentally, since the cable is shielded its outer jacket is thicker, thus more abrasion resistant than unshielded cables.
The Solution
After reviewing the primary criteria as well as the requested cable construction of AWG18-20 with 4-8 conductors, the HELUKABEL team went to work evaluating the best product offering from its extensive product portfolio. The MEGAFLEX® 500-C quickly rose to the top of the cables that would best fit this unique application. This flexible, UL/CSA-approved control cable satisfies not only the requirements of the manufacturer but is also highly flame retardant, resistant to oils and greases, ozone resistant and contains no silicone. It’s -40°C to 80°C temperature range is more than adequate for this hazardous, underground application. Finally, with a tensile strength rating in excess of 2,000 psi., MEGAFLEX® 500-C has the durability to withstand many types of challenging environments.
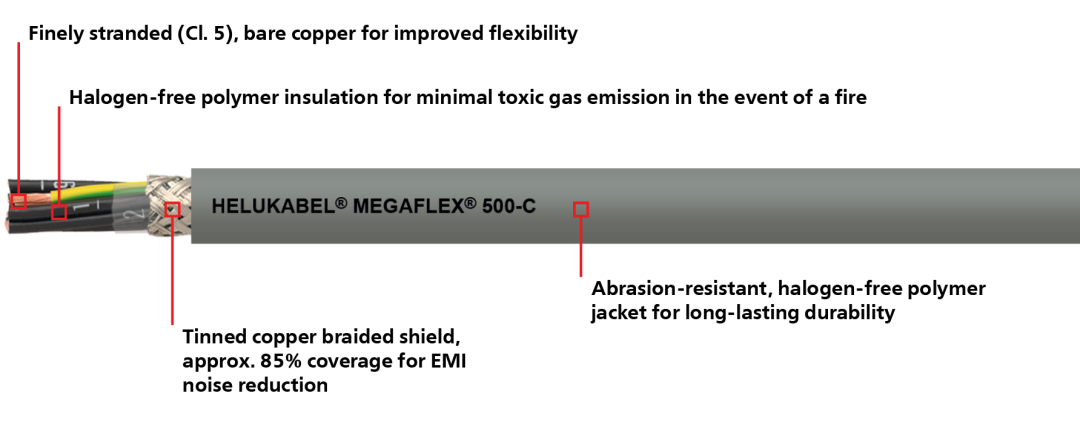
Since the manufacturer provides services to mining companies around the globe, the cable would be used on vehicles in multiple nations. While already approved for use in the United States, Canada and Europe, the company had to submit samples and work with HELUKABEL to provide the necessary documentation to supply to their end users for localized testing and verification. With the approval processes deemed successful, the MEGAFLEX® 500-C cable was accepted and specified for use out in the field.
ARTICLE DOWNLOAD
Click here to view this article in our digital download centre.