Food Production on a Whole New Level
Vertical farming - the cultivation of food in multi-story greenhouses - is considered one of the most exciting trends in food production. A pioneer in this field is the Romanian start-up Ultragreens. In their highly automated indoor farms, the company relies on top-quality and thoroughly tested solutions from HELUKABEL for the reliable transmission of power, signals and data.
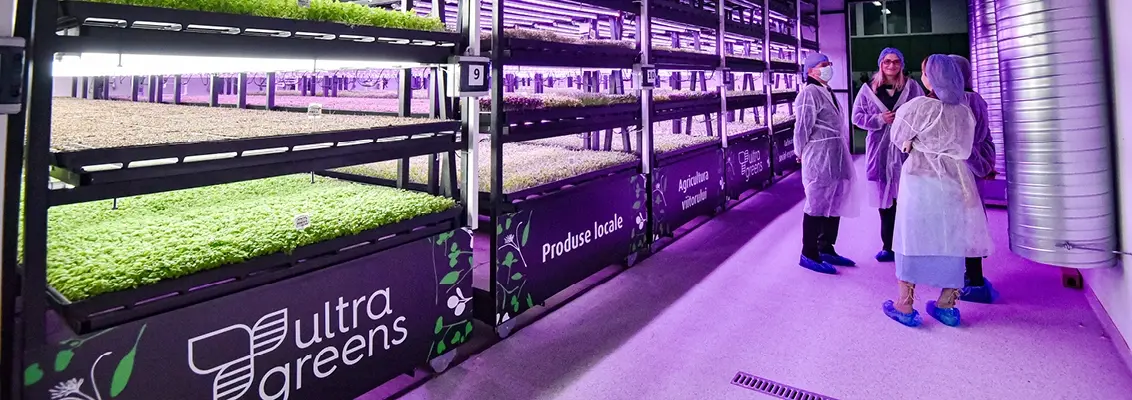
Ensuring a sustainable food supply is one of the greatest challenges facing humanity in the coming years and decades. Experts estimate that the world's population will grow to 9.7 billion people by 2050, and so the demand for food is also expected to increase rapidly. Meanwhile, food production is already a big contributor to environmental problems, climate change is causing crop failures and political conflicts are affecting supply chains. Innovative ideas are needed to ensure that humanity can continue to feed itself sufficiently in the future.
An extremely promising approach is so-called vertical farming, the cultivation of plant-based foods in multi-story buildings. With this technology, the space required for production is reduced, allowing for huge leaps in efficiencies and making vertical farming particularly interesting for urban areas. In addition, the plants are protected from extreme weather in the closed greenhouses and grow under controlled conditions, improving harvest forecasts and results.
From compact greenhouses to indoor farms
A pioneer in this field is the Romanian company Ultragreens. Founded in 2014, the start-up is committed to growing food in closer proximity to points of sale. To do this, it relies on compact greenhouses that can be directly placed in supermarkets, for example. However, Ultragreens also plans and implements so-called green hubs: huge vertical indoor farms that are operated, for example, by nationwide wholesalers and retail chains. To optimize transport costs and reduce environmental impacts, the green hubs are often located in the immediate vicinity of retailers’ logistics centres.
Vegetables, leafy greens, herbs, or seedlings, also known as microgreens, can be grown in the greenhouses. These are young vegetables that grow up to 10 centimeters high and can only be harvested after one to two weeks. Their high vitamin and mineral content make these plants real superfoods. In addition, the short production process enables consistently high yields at any time of year. "We are convinced that vertically grown microgreens are one of the keys to solving the challenges of global nutrition in the future," explains Cristian Tudor, co-founder and CEO of Ultragreens.
A high level of automation increases efficiency
Several green hubs are already operating successfully in Romania, and the company recently announced its entry into the Bulgarian market. The vertical greenhouses are very modern and fully automated. The plants grow under precisely calibrated LED light and without soil in so-called hydroponics, where they are supplied with all the necessary nutrients through special substrates. Irrigation, ventilation, temperature and many other factors are precisely regulated by computer systems and continuously monitored with comprehensive sensor technology. If a limit value is exceeded or not reached, the system adjusts itself automatically so that optimal growing conditions always prevail. "The extensive technical equipment with sensors, control and monitoring systems is of course essential for the operation of our vertical farms," describes Tudor. "On the other hand, it also means that malfunctions or failures of individual components can affect the entire harvest."
To avoid this, Ultragreens only equips its systems with high-quality, reliable components that have been extensively tested beforehand. For the cabling, the company has relied on HELUKABEL since the very beginning. The electrical connection technology specialist supplies the connection, control and data cables required for the operation of the vertical greenhouses. Tried and tested solutions such as the JZ-500 and JZ-600 cable types, the H07V-K single conductors or the TRONIC-CY data cable are applied.
All expectations met
"For us, quality was the most important criterion when selecting our suppliers," reports Cristian Tudor. "HELUKABEL was recommended to us by one of our technical service partners - and met our high expectations." The HELUKABEL Romania team, led by Managing Director Ionut Nica, thoroughly examined the application and selected the optimal solutions for the special operating environment. "Importantly, the cables used must be resistant to moisture, and they must also be sufficiently bendable to allow for a flexible installation even in tight spaces," explains Nica.
Those responsible at Ultragreens value having a competent contact partner directly in their own country, who reacts quickly and purposefully to enquiries. All cables supplied by HELUKABEL are also certified according to the standards and regulations applicable to the local market. "HELUKABEL is more than a supplier to us, they are a partner for the joint development of our product portfolio," praises Tudor. Further projects are already being planned - for example, the largest vertical greenhouse in Europe to date, with a cultivation area of 6,500 square meters on 12 levels. "Our goal is to play a major role in shaping this new type of agriculture," Cristian Tudor emphasises. "And HELUKABEL's support is key to our success."
You can also find this and many other exciting articles in the current issue #13 of our customer magazine POWER. Read it now!